CNC machining is one of the most common manufacturing methods used to manufacture parts and products. The use of Computer Numerical Controls (CNC) allows parts to be manufactured using a highly automated process, which has the upper hand on many conventional manufacturing methods in terms of speed, production rate and accuracy. However, determining the right material for the process can be a daunting task.
Numerous factors should be considered when picking a material for a part or product, including workability, price, corrosion resistance, strength, weight and cosmetic appearance. While there are hundreds of metals and alloys that can be used for CNC machining, let’s take a look at the most common ones to consider:
- Aluminum 6061 – This is the most common general-purpose aluminum grade and its typically used for auto parts, bicycle frames, sporting goods, frames for RC vehicles and more. Similar to other aluminum alloys, it has a good strength-to-weight ratio and is naturally resistant to atmospheric corrosion. While this material has great workability and machinability, it can be pricier than other metals. It also doesn’t perform as well when exposed to salt water or other chemicals, which is something to keep in mind depending on the use of the product.
- Aluminum 7075 – On the higher end of aluminum grades, 7075 is one of the strongest aluminum alloys. Unlike 6061, aluminum 7075 has average workability due to its strength, making it hard to bend into difficult and complex shapes. The material is ideal for high-strength recreational equipment, and automobile and aerospace frames – applications that require a metal that will undergo regular stress. However, it should be avoided in cases where welding is required.
- Brass – Brass is commonly found in plumbing fitting like faucet, towel hanger, home décor and musical instruments largely due to its soft material and easy workability. Due to Brass’s high polish, it is often found in cosmetic applications and makes for a nice material to use for home décor. It also doesn’t spark when struck with another metal, making it ideal for use in environments that are potentially explosive. Free-cutting brass historically had added lead to help with machining but can now be found without lead. Naval brass is typically much harder to machine than ‘free-cutting’ brass, but it can be polished very highly. It is also naturally resistant to corrosion at sea. We use brass to make multi-spindle CNC machine fixture.
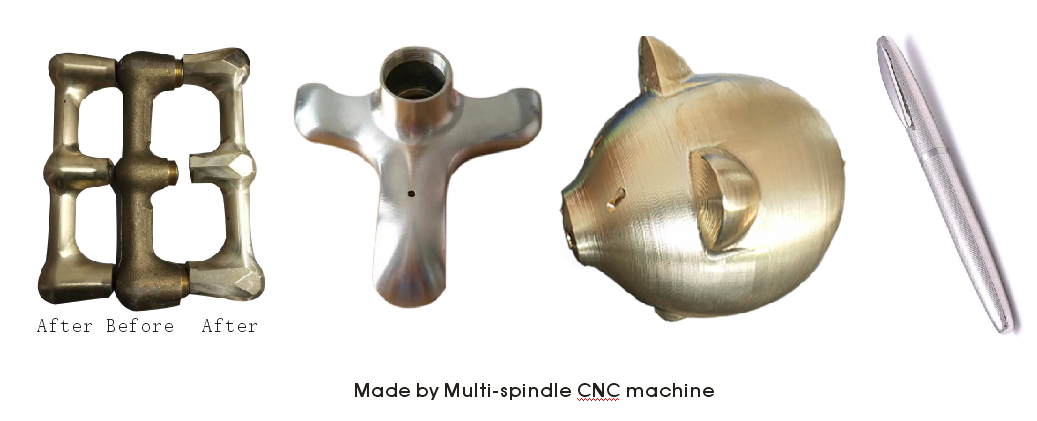
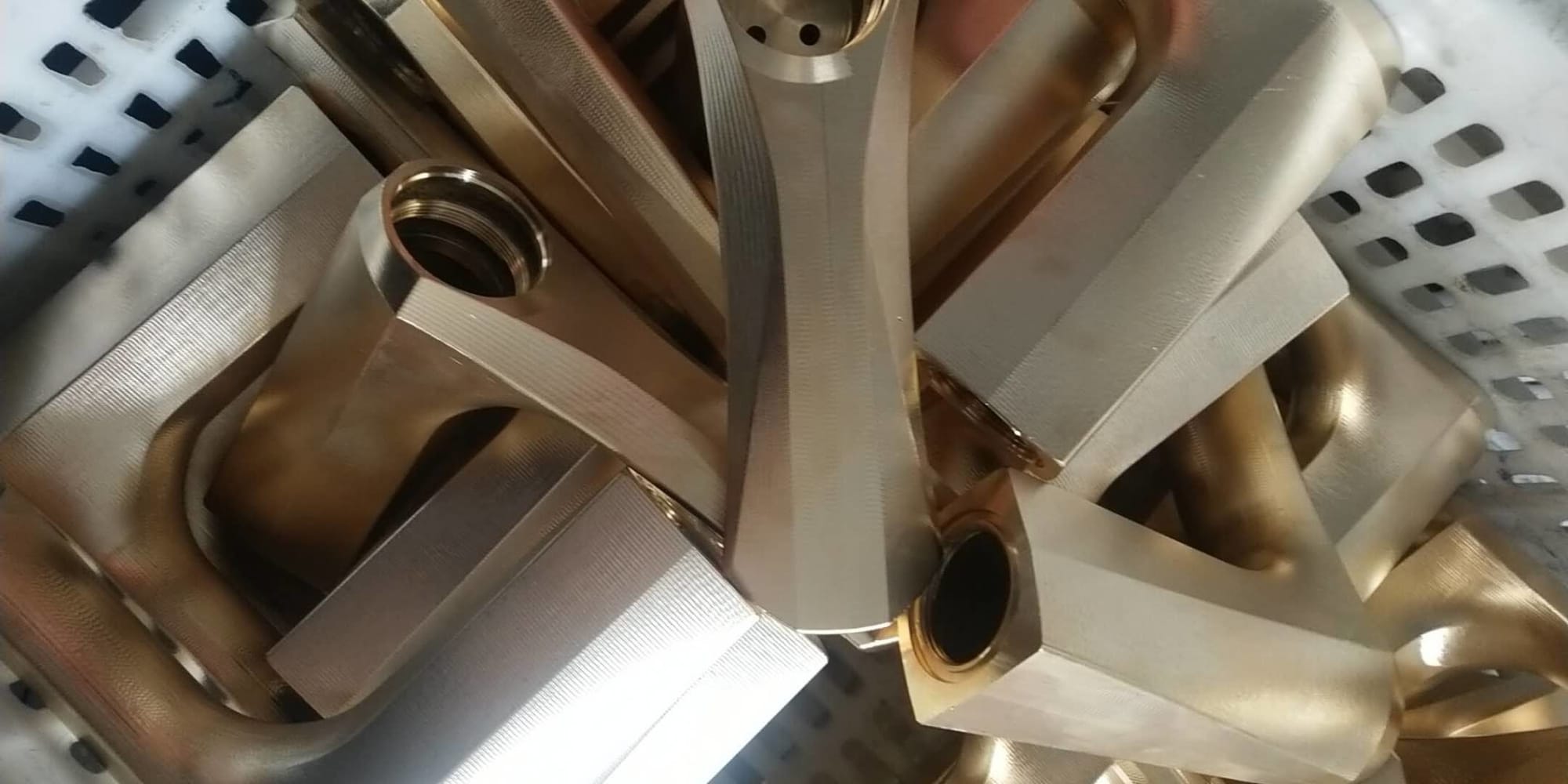
- Magnesium AZ31 – An alloy with aluminum and zinc, magnesium AZ31 is up to 35 percent lighter than aluminum with the equivalent strength. However, this material is typically more expensive and is often used for aircraft components. While the material is easy to machine, it has flammable properties. Due to its light weight and high strength capabilities, it’s also often used for laptop cases, power tools, camera bodies and other uses around the house.
- Stainless Steel 303 – Perhaps the most important thing to know about stainless steel 303, is that it looks very similar to other stainless steels, so it’s vital to test the material to ensure it actually is stainless steel 303. Other stainless-steel materials can rest very easily, which is not ideal for products. Due to the sulfur used to make the material, stainless steel 303 is not ideal for cold forming or being heat treated. This material is most often used for nuts, bolts, shafts and gears.
- Stainless Steel 304 – Stainless Steel 304, sometimes referred to as 18/8, is the most common form of stainless steel. 304 is very tough, non-magnetic, readily machinable and typically corrosion resistant making it ideal for kitchen accessors, tanks and pipes used in industry, architecture and automotive. It is found in a wide variety of consumer and industrial parts and products. 303 and 304 stainless are almost the identical metallurgy, 303 usually has a small sulfur content to aid with machining and is typically only for round bar stock; whereas 304 is mostly for sheet, plate, and flat stock. These two materials are effectively interchangeable.
- Stainless Steel 316 – Often considered a marine-grade stainless steel, 316 is tough and easy to weld. The material is very corrosion resistant making it ideal for architecture, marine fitting, industrial pipes and automotive purposes.
- Japanese D2 Steel – D2 steel is an air hardening, high-carbon, high-chromium tool steel, which has high wear and abrasion resistant properties. It is heat treatable and offers a strong hardness range. D2 Steel is ideal for creating parts and products that need to be easily bent, but also hard.
- Carbon Steel 1045 – This strong and tough material is a grade of mild steel, which is often less expensive than stainless steels. The material can be hardened, and heat treated, making it easy to machine and weld. It’s most often used in industrial applications and mechanical parts that require a high degree of toughness and strength such as for nuts and bolts, gears, shafts, and connecting rods.
- Titanium – Perhaps most well-known for its high strength, light weight and toughness, titanium can be easily welded and anodized for protection and appearance. However, it doesn’t polish well and is a poor conductor of electricity, although it is a good conductor of heat. This material is typically more expensive than other metals. It is abundant in the Earth’s crust, but hard to refine. It’s most commonly used for military, aerospace, industrial and bio-medical applications.It is used for high quality titanium eyewear making machine.
Whether you’re designing custom putters, appliances for the kitchen, or industrial equipment for aerospace uses, there is likely a material that can be CNC-machined to achieve your design. This list a quick snapshot of the most common materials used to design products for CNC machining, however, there are many more to choose from. To ensure you’re choosing the most accurate and efficient material, work closely with a manufacturer that can guide you through the process.